TOKO AWS E7018 LH Welding Rods
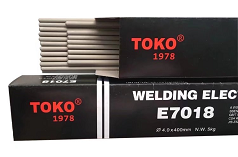
TOKO AWS A5.1 E7018 is a carbon steel stick electrode designed with a low-hydrogen potassium coating, ideal for critical welding applications
requiring minimal hydrogen-induced cracking. Classified as a "low-alloy"
electrode, it incorporates trace alloying elements to enhance mechanical strength and durability.
TOKO AWS E6013 Welding Electrode
Typical Applications
✔Heavy-Duty Construction: Bridge girders, crane booms, and structural steel frameworks.
✔Industrial Machinery: Repair and fabrication of mining equipment, hydraulic presses, and agricultural implements.
✔Shipbuilding: High-integrity welds on marine-grade steel plates and offshore platforms.
TOKO AWS A5.1 E6013 is a versatile, low-carbon steel stick electrode designed for general-purpose welding. Featuring a titanium-based flux coating, it combines ease of use with reliable performance, making it ideal for both professional welders and beginners.
TOKO AWS E6011 Welding Electrode
TOKO AWS A5.1 E6011 is a cellulose potassium-coated carbon steel electrode engineered for versatile, high-penetration welding. Renowned for its adaptability to challenging conditions, this rod excels in vertical and overhead positions, even on rusty or poorly prepared surfaces.
TOKO AWS E309L Welding Electrode
TOKO E309L-16 is a low-carbon, molybdenum-enhanced stainless steel electrode optimized for welding dissimilar metals and corrosion-resistant overlays. With a balanced 23% chromium/13% nickel composition, it minimizes carbide precipitation while offering exceptional crack resistance in multi-material applications.
TOKO E71T-1C Flux Cored Welding Wire
TOKO AWS A5.20 E71T-1C flux-cored welding wire is a versatile, gas-shielded consumable engineered for high-performance welding across industrial and
structural applications. Classified under AWS A5.20, this wire features a flux core that generates a protective slag layer and stabilizes the arc, while
relying on an external shielding gas (typically 100% CO₂ or a 75% Argon/25% CO₂ mixture) to safeguard the weld pool from atmospheric contamination.
TOKO E81T1-K2C Flux Cored Welding Wire
TOKO AWS A5.29 E81T1-K2C is a CO₂ gas-shielded, low-temperature flux-cored welding wire designed for joining high-tensile steel (550 MPa / 560 N/mm²) in cryogenic environments down to -60°C. Classified under AWS A5.29, this nickel-alloyed wire (1.5% Ni) ensures exceptional notch toughness and crack resistance in extreme conditions, maintaining ductility and strength in critical applications.
TOKO EM12K submerged ARC welding (SAW) wire
TOKO AWS A5.17 EM12K submerged ARC welding (SAW) wire, submerged arc welding process or also known as SAW welding is an automatic and high productivity fusion welding process. Compared to the Stick welding or SMAW process, granular flux in the process is laid on the unwelded seam area, designed for robust single-pass welding of mild and low-alloy steels.
TOKO ER5356(AIMg5)Welding Wire
TOKO AWS A5.10 ER5356 (AIMg5) is a versatile aluminum-magnesium filler metal containing approximately 5% magnesium, designed for both MIG (GMAW) and TIG (GTAW) welding processes. Classified under AWS A5.10, this alloy delivers exceptional corrosion resistance in marine and saltwater environments, making it ideal for applications where durability against harsh conditions is critical.
TOKO AWS A5.18 ER70S-6 (SG2) is a high-deoxidizer carbon steel MIG (GMAW) welding wire, engineered with elevated manganese (Mn) and silicon (Si) content to combat
porosity in environments with moderate surface contaminants like mill scale, rust, or oxidation. Classified under AWS A5.18, this wire ensures reliable
performance on carbon steels where pre-weld cleaning is limited, making it a practical choice for industrial and fabrication settings.
TOKO 2535Nb NiCr Alloy Welding Rods
TOKO 2535Nb is a premium nickel-chromium alloy engineered to deliver exceptional performance in extreme environments. Combining outstanding corrosion resistance, high-temperature strength, and superior creep resistance, it is tailored for demanding applications across aerospace, chemical processing, and energy sectors.
TOKO AWS A5.28 ER80S Ni2 TIG Rods
TOKO AWS A5.28 ER80S Ni2 is a copper-coated, low-alloy solid wire engineered for gas metal arc welding (GMAW) of high-strength, low-temperature steels. Designed to AWS A5.28 standards, this wire delivers exceptional arc stability, smooth metal transfer, and minimal spatter under optimal welding conditions, ensuring consistent, high-quality welds even in demanding applications.
TOKO Submerged ARC Welding Flux
TOKO fluxes (e.g., SJ101, SJ301, SJ501) are granular, agglomerated fluxes designed for submerged arc welding (SAW) applications. These fluxes serve multiple critical functions:
Download MTC data
AWS A5.1E6010, AWS A5.1
E6011, AWS A5.1
E6013, AWS A5.1
E7016, AWS A5.1
E7018, AWS A5.28
ER80S-Ni2, AWS
MIG
ER430, AWS
TIG 310S, AWS
MIG 307Si, AWS A5.4
E307-16, AWS A5.4
E308L-16, AWS A5.4
E309L-6, AWS A5.4
E310-16, AWS A5.4
E316L-16, AWS A5.4
E312-16, AWS A5.4
E347-16, AWS A5.20
E71T-1C, AWS A5.20
E71T-5C, AWS A5.20
E71T-GS, AWS A5.29
E81T1-K2C, AWS A5.29
E718-K6, AWS A5.9
ER2535Nb, AWS A5.4
E2535Nb,
AWS
A5.4
E3545Nb, AWS A5.14
NiCrMo-3, AWS
A5.11
NiCrMo-3, AWS
A5.14
NiCrMo-10, AWS A5.9
E2209, AWS A5.4
E2209-15, AWS A5.15
ENiFe-CI, AWS A5.15
ENi-CI, AWS A5.14
ERNiCrMo-3(6625), AWS A5.10
ER4043, AWS A5.10
ER5183, AWS A5.22
ER5356, AWS A5.22
ER308LT1-1. AWS A5.22
ER309LT1-1, AWS A5.22
ER316LT1-1, AWS A5.17
EM12K, AWS A5.18
ER70S-6, AWS A5.18
ER70S-3, AWS
A5.15 T Fe15, Welding Flux:
Technical Advantages
✔Smooth Arc Stability: Delivers consistent arc ignition and minimal spatter, even on rusty or painted surfaces.
✔Effortless Slag Removal: Titanium flux generates a thin, self-peeling slag layer for clean, high-quality welds.
✔Multi-Position Welding: Optimized for flat and horizontal positions, with limited usability in vertical-up applications.
Technical Advantages
✔Deep Penetration: Cellulose flux generates forceful arcs for robust root passes and joint penetration.
✔All-Power Compatibility: Optimized for AC and DC+ polarity (recommended: 80-140A).
✔Slag-Free Performance: Produces clean, spatter-minimized welds ideal for multi-pass applications.
✔Positional Flexibility: Master vertical-up, overhead, and horizontal fixed-pipe welding with ease.
Technical Advantages
✔Low-Carbon Formula: ≤0.04% carbon content prevents intergranular corrosion in sensitization-prone environments (400-850°C).
✔All-Position Control: Rutile coating ensures stable arcs in vertical-up, overhead, and restricted-access welding.
✔Corrosion Defense: Ideal for mildly aggressive environments (pH 3-10) like food processing tanks and chemical piping.
Technical Advantages
✔Dual gas compatibility: Effective with 100% CO₂ for cost efficiency or a 75% Ar/25% CO₂ mix for smoother arc performance and reduced spatter.
✔High deposition rates: Enhances productivity in single- and multi-pass welds.
✔Atmospheric resilience: Consistent performance in windy or outdoor settings due to the combined gas and slag shielding.
Technical Advantages
✔Cryogenic Performance: Optimized weld metal chemistry delivers superior impact toughness (Charpy V-notch tested) at temperatures as low as -60°C in the as-welded state.
✔Gas Shielding: Compatible with 100% CO₂, ensuring robust protection against atmospheric contamination.
✔All-Position Welding: Provides stable arc control, minimal spatter, and smooth bead appearance for vertical, overhead, and horizontal welding.
Technical Advantages
✔High-Deposition Efficiency: Optimized for single-pass butt and fillet welds, ideal for high-speed fabrication of structural components.
✔Enhanced Mechanical Properties: Higher carbon content boosts tensile strength, while manganese and silicon refine weld metal integrity and oxidation resistance.
✔Smooth Arc Performance: Delivers stable arc characteristics and excellent bead appearance across flat and horizontal positions.
Technical Advantages
✔Superior Corrosion Resistance: The magnesium-enriched weld deposit resists pitting and oxidation in saline or chemically aggressive environments, outperforming many standard aluminum alloys.
✔Compatibility: Optimized for welding aluminum base metals such as 5050, 5052, 5083, 5356, 5454, and 5456, commonly used in marine, automotive, and structural applications.
✔Aesthetic Finish: Produces a clean, white post-anodizing color match, ideal for architectural or visible welds requiring a uniform appearance.
Technical Advantages
✔Enhanced Deoxidation: High Mn/Si levels neutralize oxygen impurities, minimizing porosity and ensuring clean, defect-free welds even on imperfect surfaces.
✔Shielding Gas Flexibility: Compatible with CO₂ (economical), Argon + CO₂ blends (e.g., 75% Ar/25% CO₂ for reduced spatter), or Argon + 1-2% O₂ (improved arc stability).
✔Mechanical Performance: Delivers a tensile strength of 70,000 psi (480 MPa) with excellent ductility, suitable for structural and dynamic load-bearing applications.
✔Smooth Arc Transfer: Produces consistent bead appearance and minimal spatter, enhancing weld quality in flat, horizontal, and vertical positions.
Technical Advantages
✔Corrosion Resistance: Excellently withstands both oxidizing (e.g., nitric acid, hot oxidizing salts) and reducing (e.g., sulfuric acid, chloride-rich) environments.
✔High-Temperature Capability: Maintains structural integrity and creep resistance at elevated temperatures, ideal for components exposed to sustained thermal stress.
✔Precipitation Hardening: Enhanced by titanium and niobium, enabling precise strength optimization through heat treatment.
Technical Advantages
✔Low-Temperature Toughness: Produces weld metal with 80ksi (550 MPa) tensile strength and superior notch toughness at temperatures as low as -60°C, ideal for cryogenic and Arctic environments.
✔Radiographic Quality: Ensures defect-free, X-ray compliant welds critical for structural integrity in pressure vessels, pipelines, and load-bearing components.
✔Enhanced Composition: Contains ~2% nickel to improve impact resistance in fine-grained and nickel-alloyed steels (e.g., ASTM A553, A517, A203).
✔Atmospheric Protection: They generate a protective gas shield and molten slag layer during welding, preventing oxygen, nitrogen, and hydrogen contamination of the weld pool.
✔Arc Stabilization: Enhance arc consistency and heat control, improving bead uniformity and reducing spatter.
✔Slag Formation: Produce a self-lifting slag that minimizes porosity, suppresses undercut, and ensures smooth weld contour for easy removal post-weld.
✔Metallurgical Control: Incorporate deoxidizers (e.g., manganese, silicon)
and alloying elements to refine weld metal chemistry, enhancing mechanical
properties like toughness and crack resistance.
AWS A5.1
E6013 MSDS